In January 2020, just one year ago, I was on the other side of the world.
It seems, in my memory, not part of the same Earth we inhabit now but a parallel universe — one in which a global pandemic hasn’t restricted our movements, making travel, not only to a different country but to something as simple as the grocery store, a performance of mask-wearing, social distancing and hand sanitizing.
But that other world, in which we lived so differently, truly was just 12 months ago. We moved about freely, and as we touched down in the airport at Luang Prabhang, the dawn sunlight glinted over the mist-covered mountains. Laos was immediately beautiful.
We were a group of students from Massachusetts College of Art, on a field course to study local textile artisans across Laos. Professor Jennifer Varekamp, current chair of the MassArt Fashion Design department, was with us. Varekamp — Jenn, to her students — had built relationships with local organizations in Laos during her sabbatical the previous year, and created a two-week course that invited students from across multiple MassArt departments to join her to learn about local textile traditions. For this reason, we had filmmakers, photographers and fashion students all gathered for the trip of a lifetime.
Vientiane is the capital of Laos, a center for education and commerce, but Luang Prabhang, located on a picturesque peninsula seven hours’ drive north, is the main tourist hub. After spending several days in Luang Prabhang, we would take buses up the winding dirt roads further northward to Luang Namtha, stopping along the way for homestays in small villages that spin, dye and weave their own cotton. Check out my Instagram Stories from the trip, all linked here.
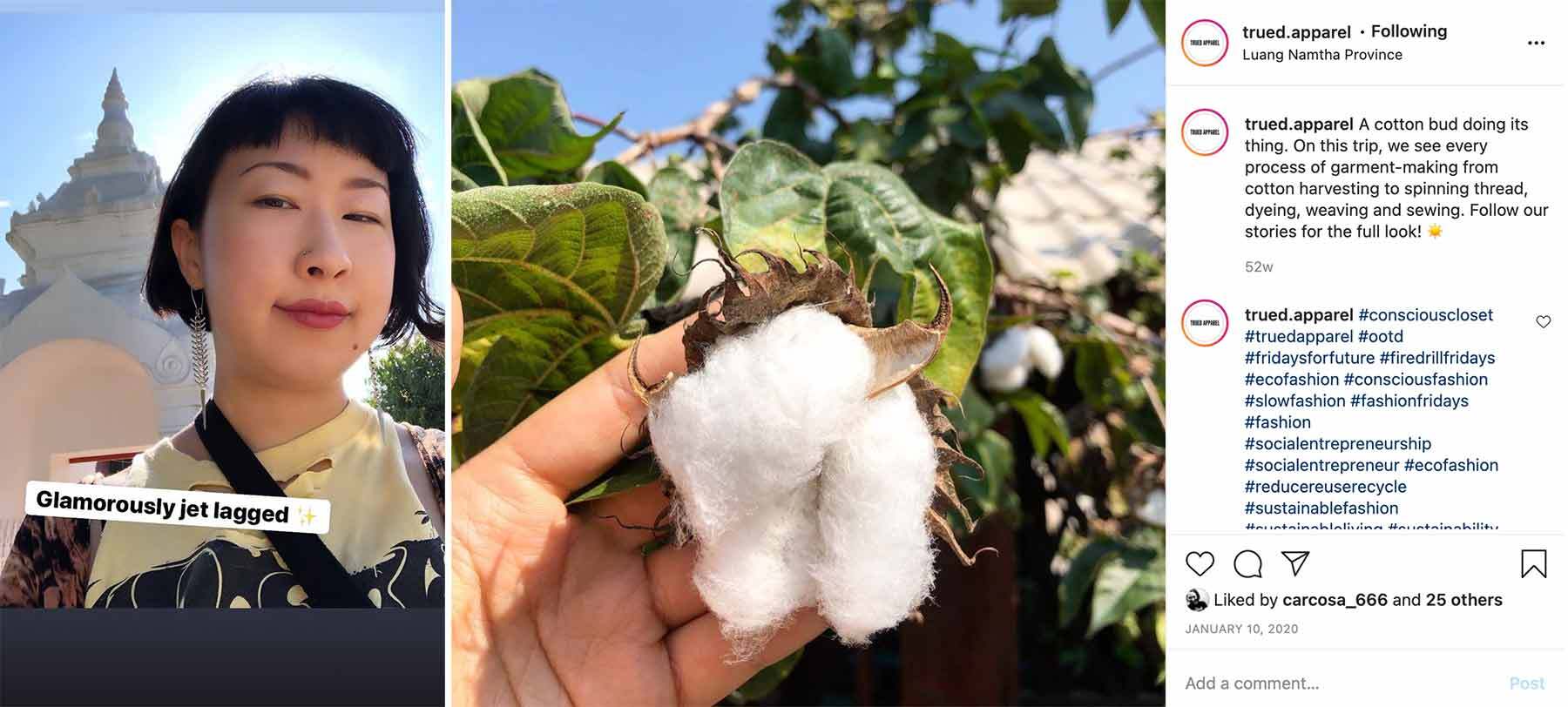
Fashion is often seen as a superfluous luxury for those with disposable income, but the industry itself has deep-rooted implications for the working class across the globe. Massachusetts and the rest of New England have a rich history in textile manufacturing and shoemaking, which makes the presentation of Made It: The Women Who Revolutionized Fashion at PEM especially resonant. As Made It demonstrates, women have a long history of organizing for their rights in an industry whose lowest paid workers are disproportionately female and whose leadership is male-dominated.
Our newly opened South Asian Art galleries are also relevant to this story. A focal point of India’s journey out from under British colonial rule was their retaining of agency and value created through textiles. In mid-century India, wearing homespun cloth rather than fabric sold to Indians by the British expressed the wearer’s solidarity with Mahatma Gandhi’s nonviolent independence movement.
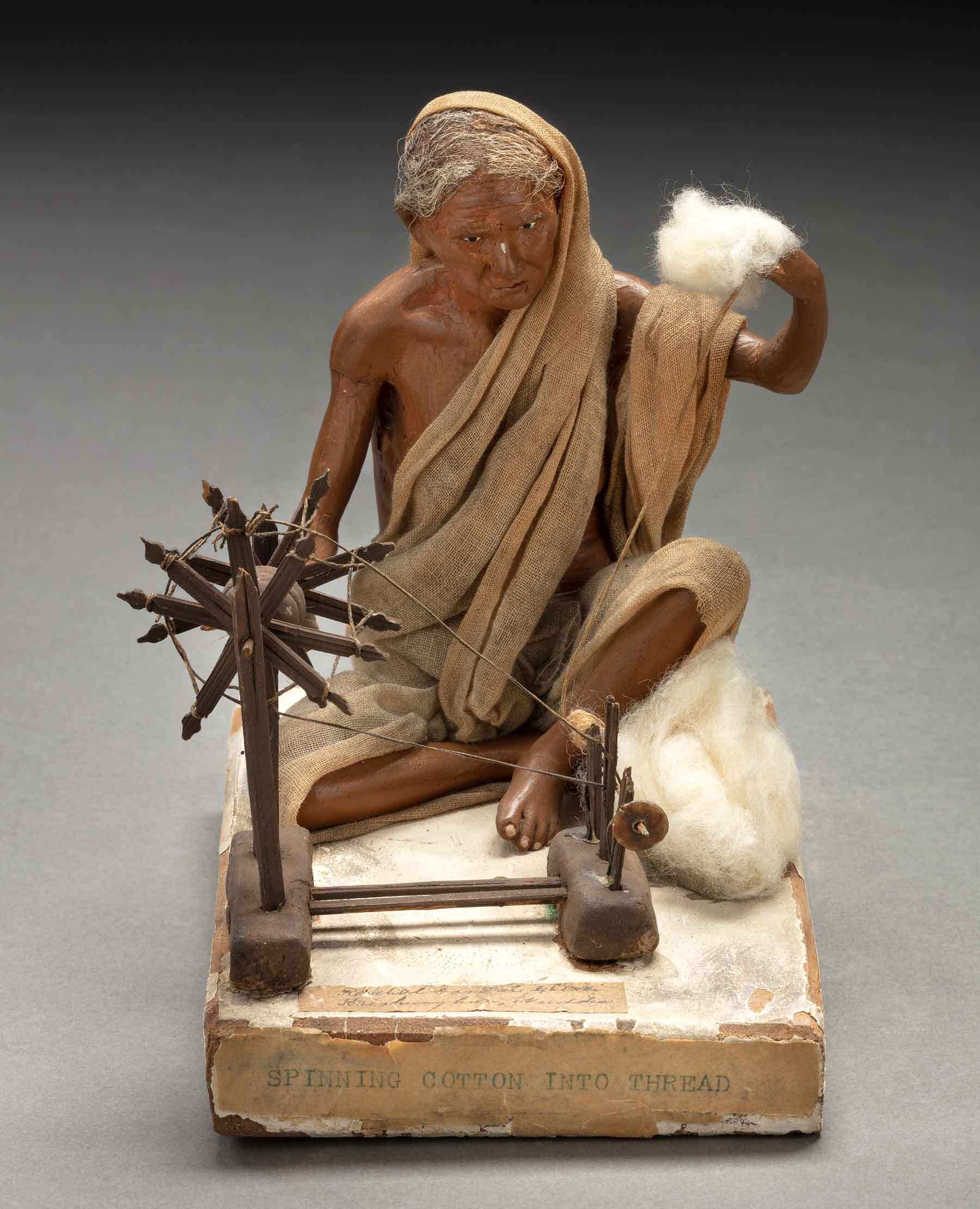
Artists in Kolkata or Krishnanagar. Woman spinning cotton, 19th century. Unfired clay, textile, paint, wood, cotton, and hair. Gift of Henry Peabody & Company, 1968. E44821.
In our own galleries, this text accompanies a sculpture of a woman at a spinning wheel:
"For every revolution of the wheel spins peace, goodwill, and love."
—Mahatma Gandhi, 1921
Artists in Kolkata or Krishnanagar. Woman spinning cotton, 19th century. Unfired clay, textile, paint, wood, cotton, and hair. Gift of Henry Peabody & Company, 1968. E44821.
An elderly woman spins cotton into thread at a charkha, or spinning wheel, demonstrating how one of India’s most coveted exports was traditionally made. What the British considered an archaic tool became a symbol of pride for the political movement that led to Indian Independence in 1947.
Mahatma Gandhi, the transformative leader of the Indian independence movement and an icon of peaceful resistance, encouraged the people of India to produce their own homespun cloth rather than buy fabric from British suppliers. By styling himself as a simple village craftsman and employing traditional techniques as an act of resistance, he inspired the diverse populations of India to unite in a common struggle for self-rule.
So we see that rather than an industry divorced from the concerns of everyday people, by virtue of being a system that controls value and power, it has in fact affected everyday people quite deeply — and continues to.
Made It: The Women Who Revolutionized Fashion showcases more than 100 works, spanning 250 years, recognizing women's often-overlooked contributions to the fashion and design industry. In the exhibition, we highlight some key moments in fashion history, a number of which are particular to New England. A short list below:
1834: Female shoe binders form a union in Lynn, Massachusetts, and demand fair wages from employers
1837: Shoe and boot manufacturers employ 18,000 women in New England
1843: Lowell Female Labor Reform Association begins public petitioning for 10-hour work day
1857: Police attack women garment workers protesting for better working conditions and higher wages in New York
1860: 3,000 workers walk off the job in New England Shoemakers Strike in Lynn, Massachusetts
1871: Mary Harris “Mother” Jones begins work as a labor organizer after her dress shop is destroyed in the Great Chicago Fire
1909: “Uprising of the 20,000” female shirtwaist makers in New York strike against sweatshop conditions
1909: First National Women’s Day, brought about by the labor actions of garment workers, is celebrated on February 28 in the U.S.
1911: Triangle Shirtwaist Factory fire in Manhattan kills 146 garment workers, including 123 girls and women
1912: 23,000 textile workers participate in the Bread and Roses strike begun by immigrant women in Lawrence, Massachusetts, leading to public outcry and a congressional investigation
Since a good portion of American manufacturing has moved abroad, we find these same concerns playing out in other countries. Many will remember the 2013 Rana Plaza Factory collapse in Bangladesh, which killed more than 1,100 garment workers.
Last January, while we were in Laos, I was gearing up to launch my sustainable fashion business Trued Apparel. I aimed to build the business ethically both in sourcing and production — meaning that not only did I want to use fabrics that are better for the environment, minimizing the use of polyester and other man-made textiles, but it was important to me that the value created from the business be shared with the people whose hands ultimately create the garments.
The fast fashion industry makes it standard practice to cut garment workers out of the profit equation. Workers are chronically saddled with unrealistic turnaround times to meet quick-moving fashion trends, untenable wages and, at times, toxic materials that can contribute to illness and birth defects. I highly recommend the documentary The True Cost, which we’ve screened previously at PEM, for an overview of how problematic fast fashion is.
The emerging slow fashion movement creates a shift in thinking away from speedy consumer capitalism towards mindfulness, understanding where the things we own come from, and having compassion for the people involved in their production. Another benefit of a living wage in the fashion industry is a gendered one; Over 85% of the 40 million garment workers worldwide are women, so to share value with them has the effect of empowering women in the places or countries in which you do business.
I had all this in mind as we visited Ock Pop Tok in Luang Prabhang, a pioneering social enterprise established in 2000 by Englishwoman Joanna (Jo) Smith and Laotian Veomanee (Veo) Douangdala that now boasts over 90 employees and 500 artisan partners throughout Laos.
Ock Pop Tok, meaning “East Meets West” in Lao, was founded on the principles of fair trade and sustainable business practices, to bring people together through textiles to exchange knowledge and ideas.
“Weaving, which is still done primarily by village women, is often considered domestic work that is not representative of progress or economic advancement,” their website reads. “By deciding to operate on fair trade principles, specifically by providing competitive wages, opportunities for continued learning and professional development, Ock Pop Tok gives weavers the ability to earn a sustainable livelihood for their families and communities.”
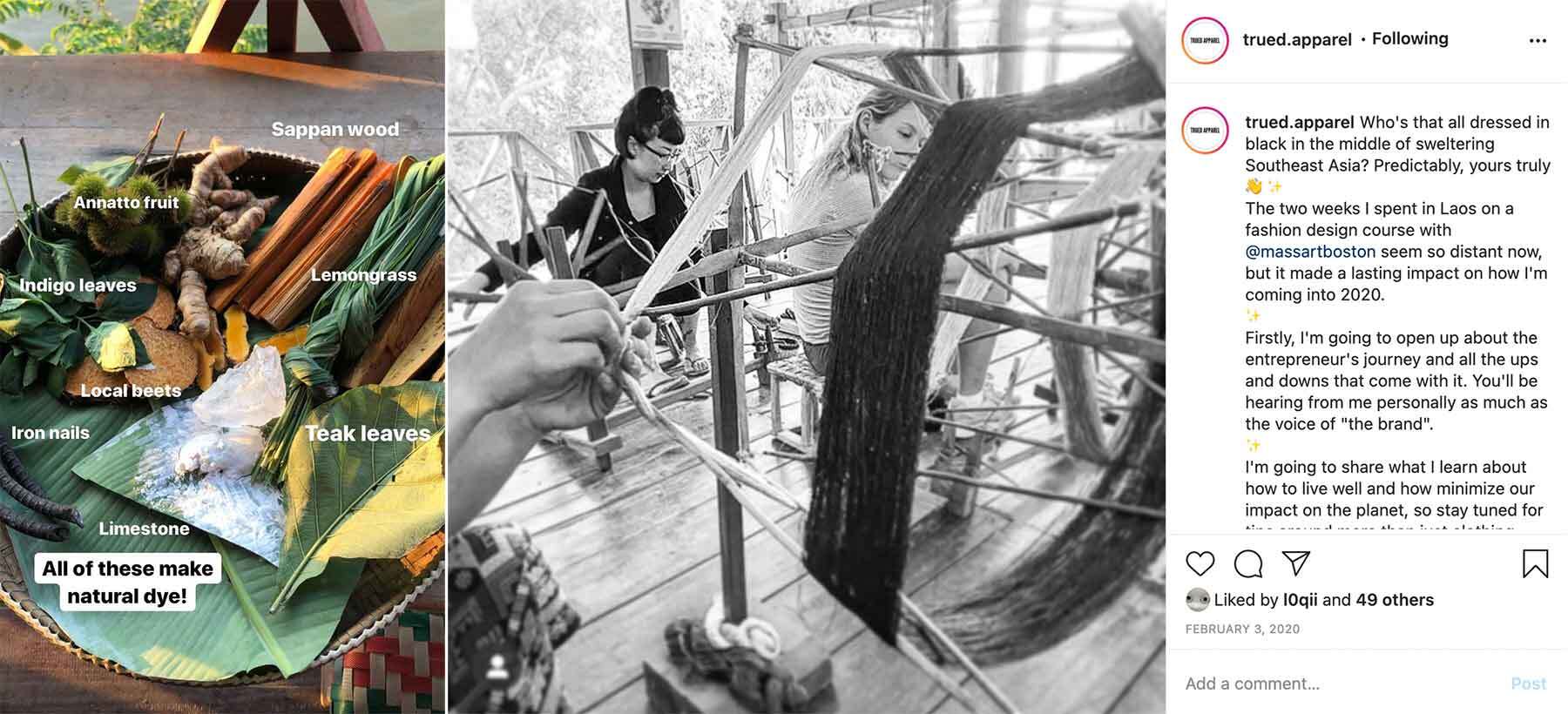
In the Ock Pop Tok Living Crafts Centre, classes are held daily to give tourists hands-on experience in creating their own Laotian textiles, from dyeing to weaving, to batik designs. With 49 recognized ethnic groups in Laos, there are many handicraft and textile traditions to share, and many stories to tell. Fifty Laotian weavers are employed both at the on-site facility and from their own home villages. Their wares, from throw pillow covers to wall tapestries, are sold in the Ock Pop Tok Shop in downtown Luang Prabhang. Their on-site Silk Road Cafe even provides local fare for visitors to have a bite between classes.
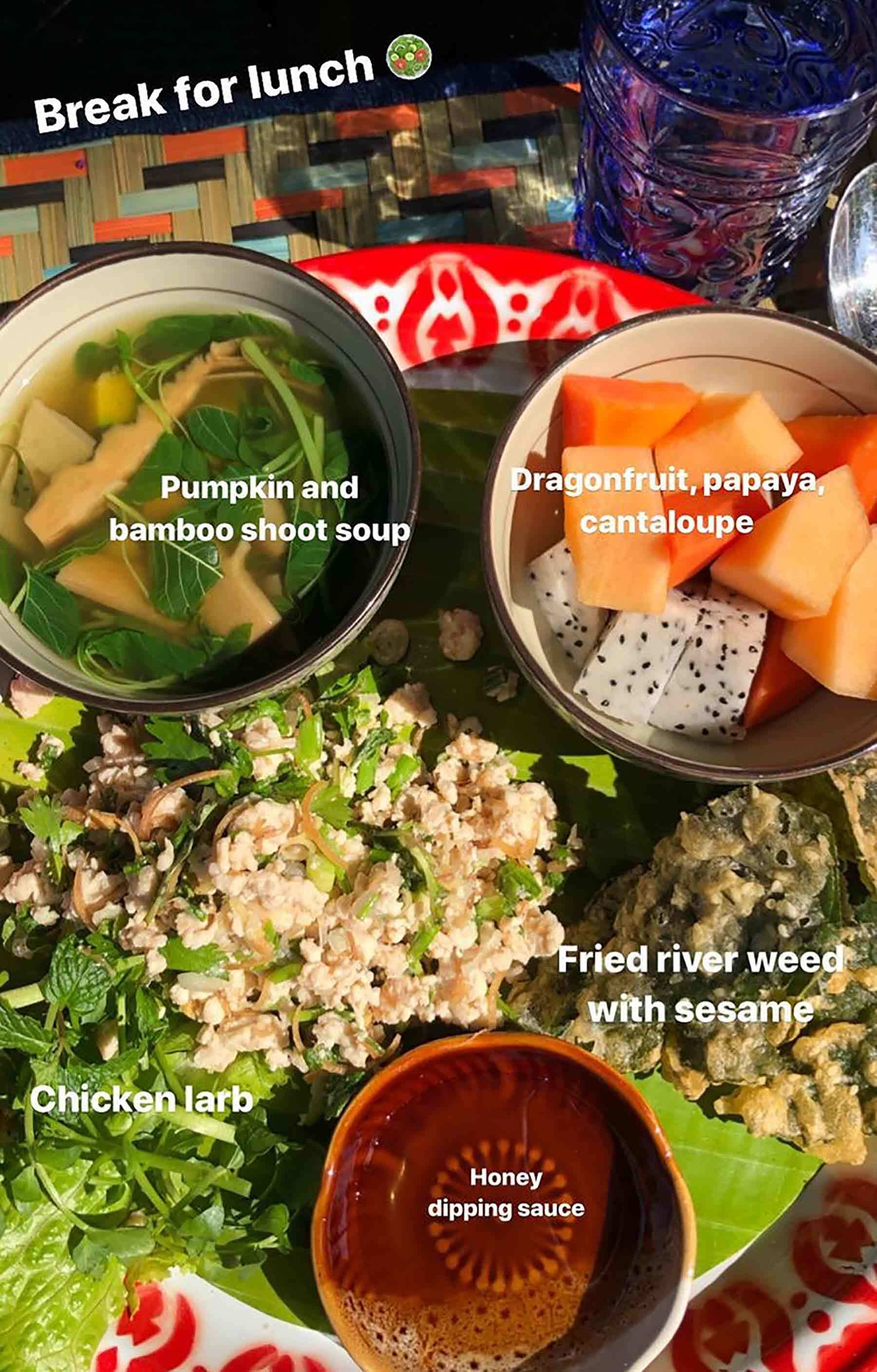
Another fantastic social enterprise we connected with was Ma Té Sai, meaning “where is it made?” in Lao. Ma Té Sai was founded in 2010 by Emi Weir and Cleménce Pabion, and are particularly focused on teaching village women how to create modern, marketable textile goods using a combination of their existing handicraft skills and sewing training provided by Ma Té Sai. Starting with funding from a Malaysian foundation, Ma Té Sai now co-creates goods with Tai Daeng, Tai Dam, Lanten, Hmong and other ethnic communities in Northern Laos that stock the shelves of their Luang Prabhang and Singapore locations. Ma Té Sai also conduct workshops and tours as part of their business, to educate visitors on the variety of ethnic textile traditions in Laos.
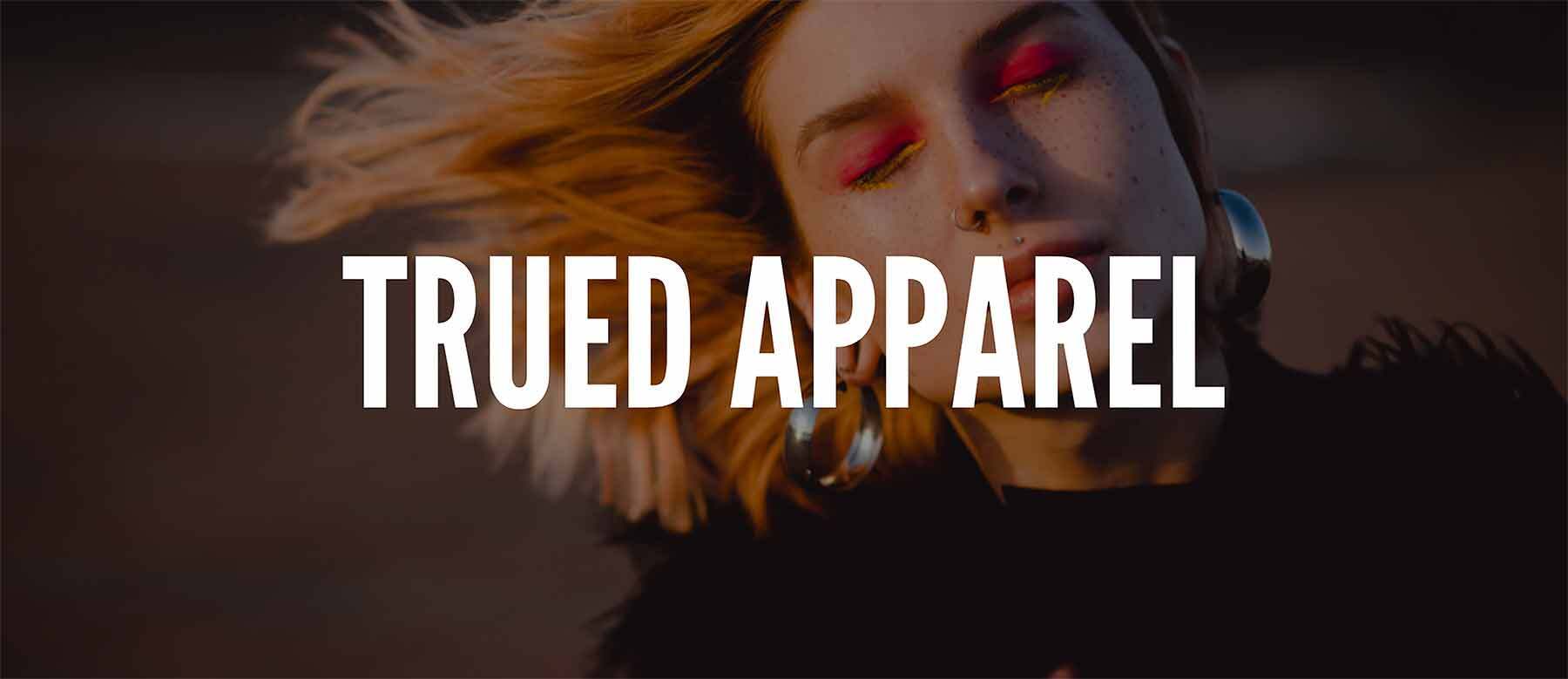
I share so much about Ock Pop Tok because this is the dream of a social enterprise: to build sustainable wealth for an entire community, to create an ecosystem that rewards rather than exploits skill, and that values people over profiteering. Trued Apparel is locally made and sustainably sourced. It’s been a long and winding journey as someone new to the industry to forge new relationships with trusted partners to create a quality product line we’re proud of. Now that we’ve launched at the end of 2020, there are only bigger dreams ahead.
Meanwhile, the Whatsapp group created with my MassArt classmates continues to light up my phone, as we share updates from our lives going into a new year. With the Covid-19 vaccine rolling out, one hopes we can travel and move about freely again before too long.
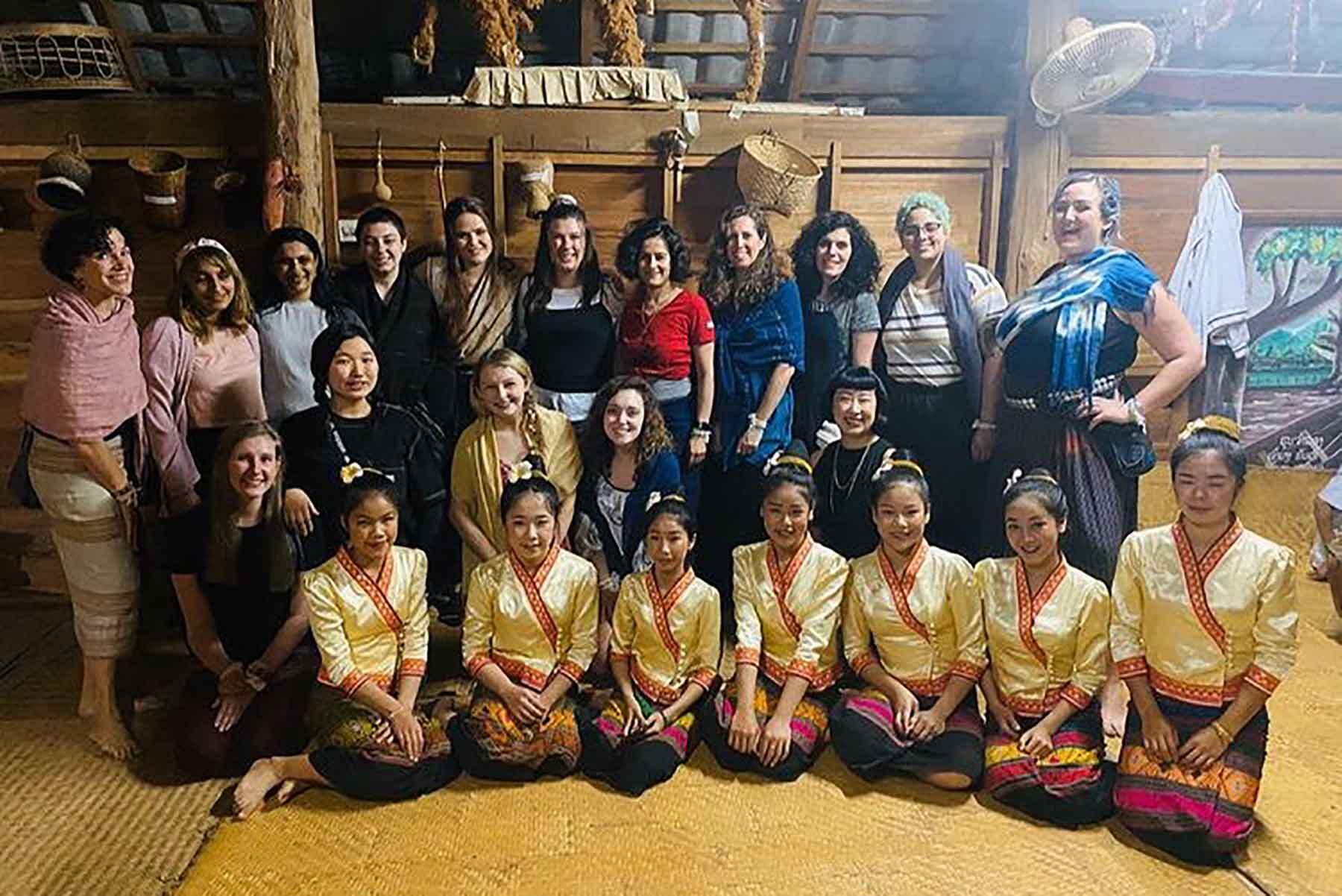
Keep exploring
Blog
The woman behind the brand
4 Min read
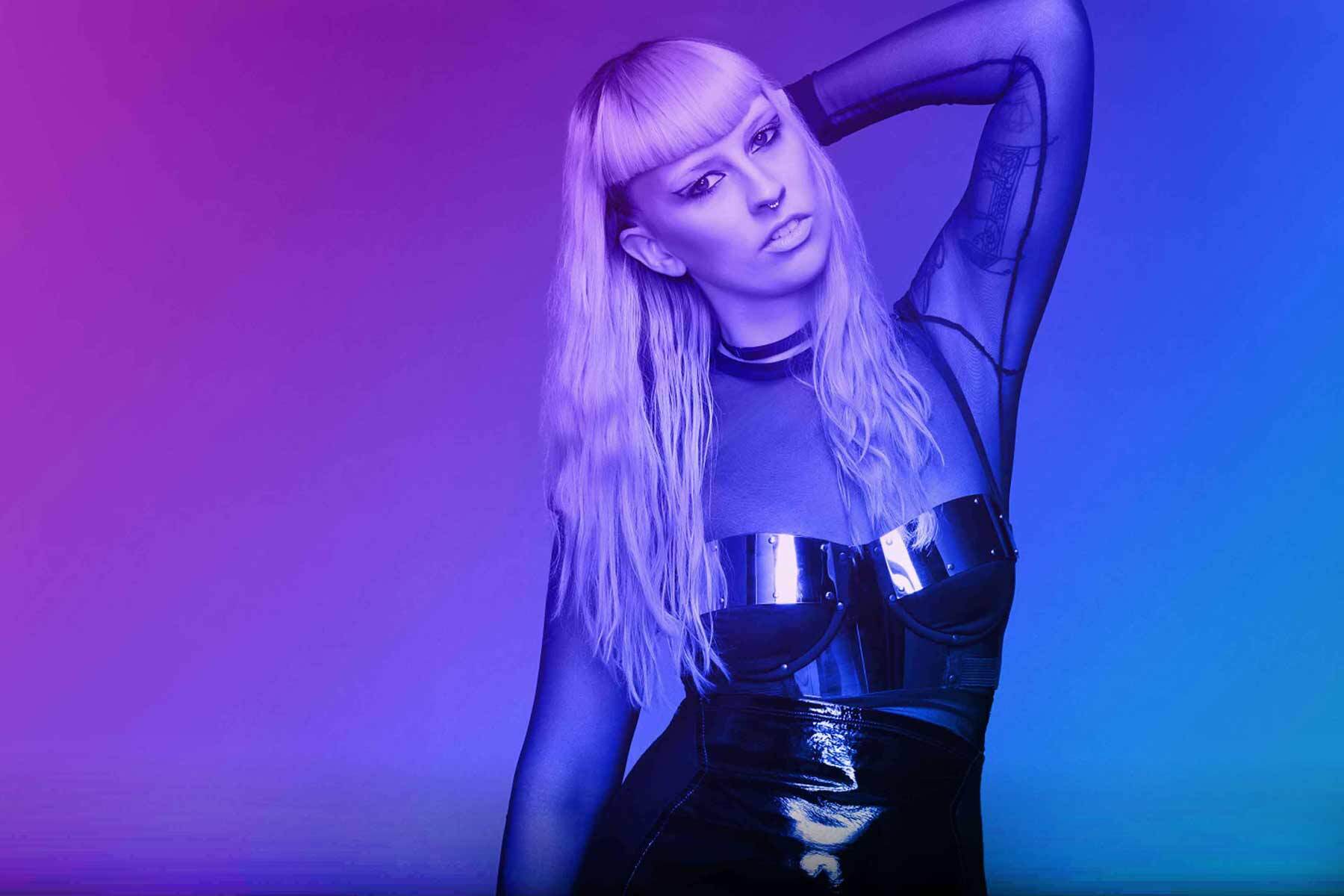
Blog
Women who made it
6 min read
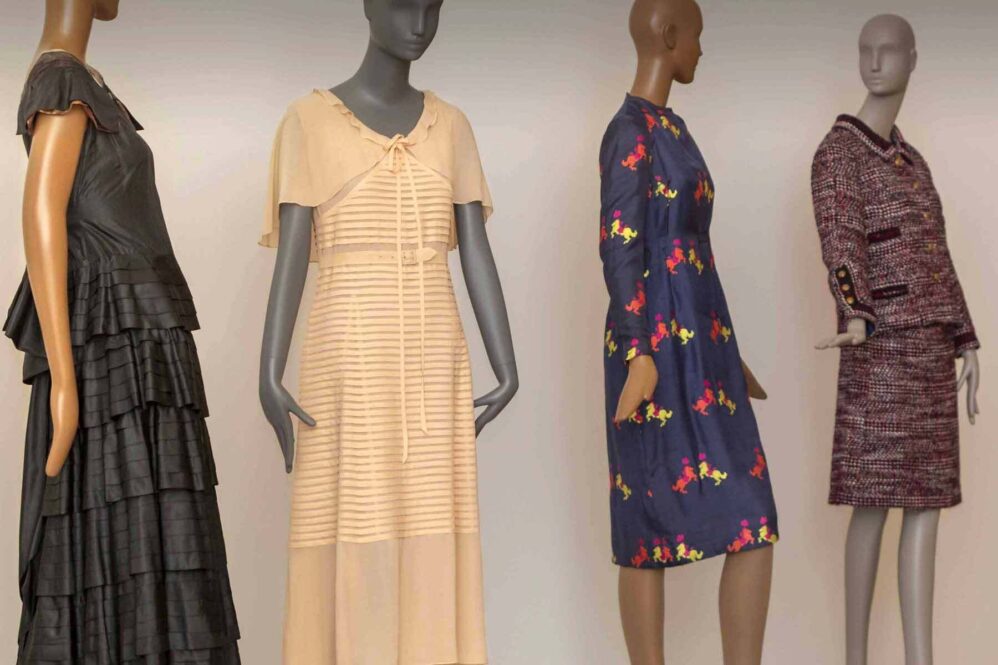
Blog
A Studio Visit With Queen Adeline
6 Min read
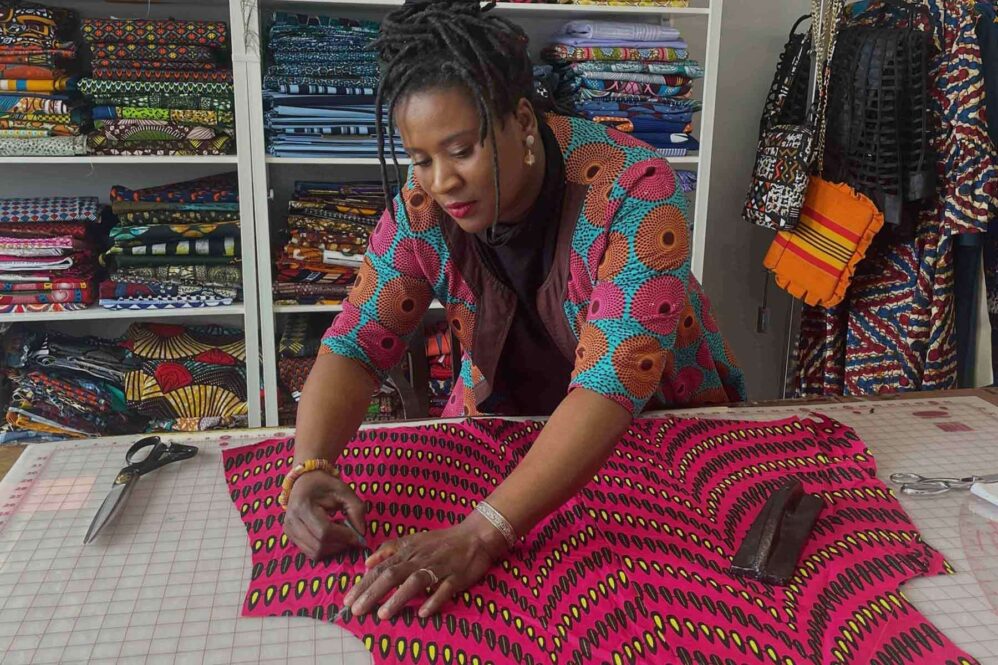
Blog
A look into how it’s made
5 min read
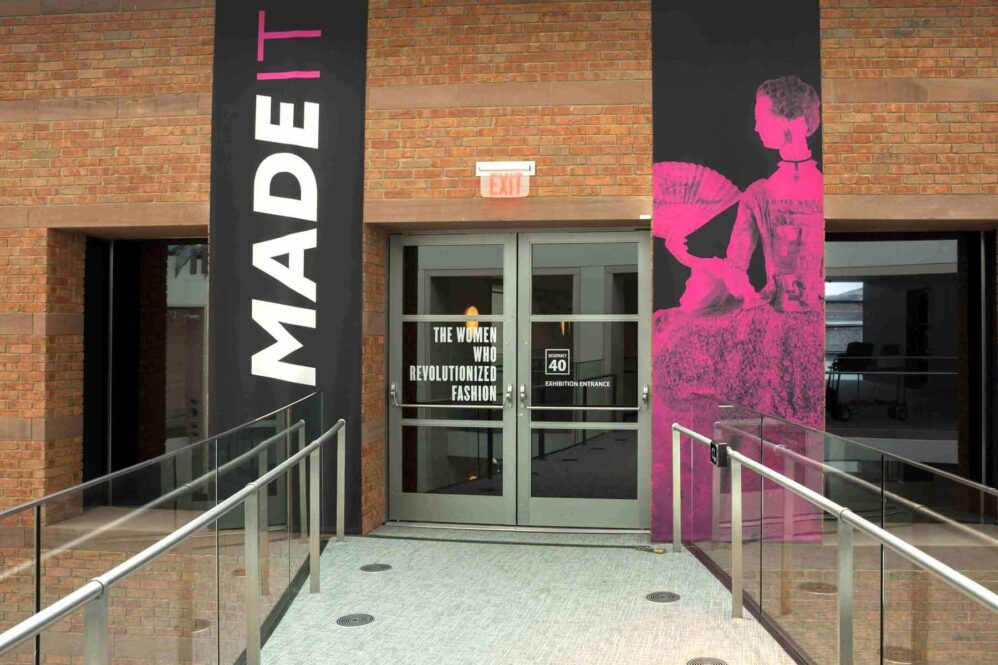